不鏽鋼經鹽浴熱處理後研磨拋光實例
PCB設備零組件研磨拋光前後比較
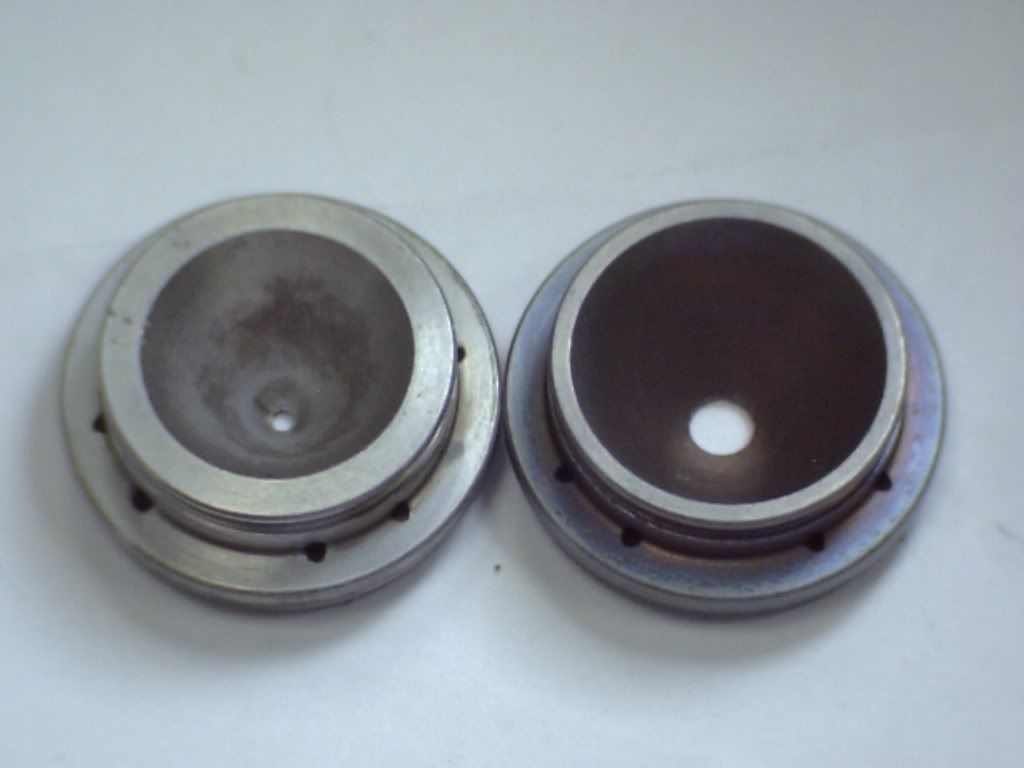
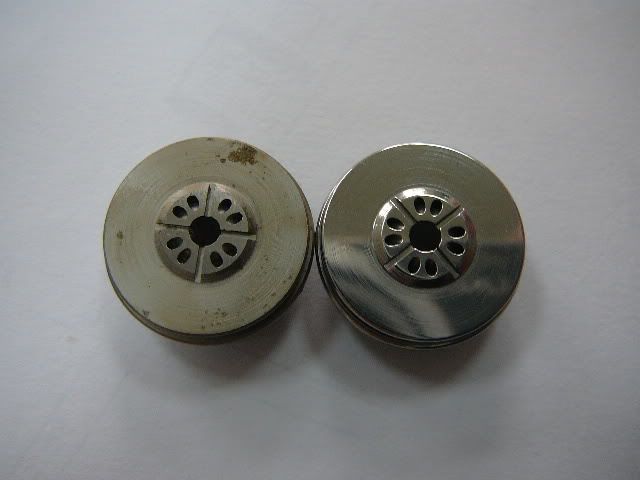
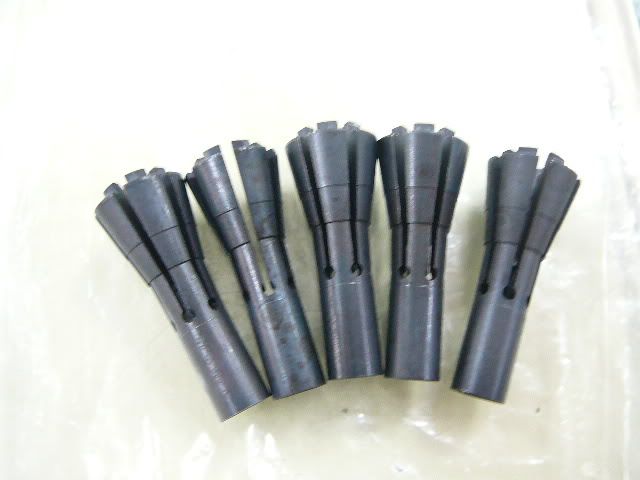
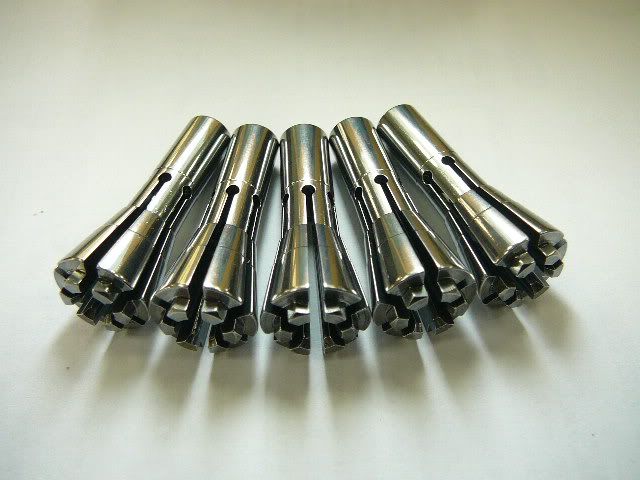
※鹽浴爐
鹽浴爐設備便宜,加熱速度快,處理件表面氧化程度低,適合小型工件熱處理用。若配合適當的鹽裕,可應用於淬火加熱、滲碳、滲氮、滲硫等表面處理。常用的鹽浴種類包括(1)使用於200℃至500℃的低溫鹽主要以硝酸鹽或亞硝酸鹽;(2)使用在450℃至950℃間的中溫鹽,主要以氯化鈉、氯化鈣及碳酸鈉的混合鹽;(3)使用在950℃至1250℃溫度範圍的高溫鹽則大多以氯化鋇鹽為主。
鹽浴熱處理一直用於工具鋼和軸承鋼等的淬火,以及馬氏體(M)等溫淬火、奧氏體(A)等溫淬火等處理。近年出現了真空熱處理和氣氛熱處理等新技術,與之比較,因鹽浴熱處理存在作業環境差、廢水處理難、爐子壽命短、生產效率低、難以批量生產等缺點,故其應用範圍正在縮小。然而,鹽浴熱處理也有應變(也稱變形)小、減少淬火龜裂發生等優點,而且能解決大型工件淬火不足的問題。因此,曾一度轉向真空處理的,再次回歸鹽浴熱處理的案例也不少。並且,始於2008年的世界金融危機造成的經濟不景氣,不得不重新評價原來長期使用的大量、高效的生產方式。因此,在展望21世紀的熱處理技術革新的過程中,重新評價了鹽浴熱處理。另外,鹽浴熱處理雖也包含液體氮(N)化、液化軟N化、熔鹽碳(C)化物包覆處理等;但本文省略了表面改質處理,僅介紹中性鹽的熱處理。
1熱處理用鹽浴的種類
金屬熱處理用中性鹽可在如下3種溫度範圍內使用:①高溫(約1000-1350 ℃);②中溫(約570-950 ℃);③低溫(約160-550 ℃)。
高溫鹽浴熱處理主要用於高速工具鋼和模具工具鋼的淬火;中溫鹽浴熱處理主要用於合金工具鋼、結構鋼、軸承鋼、彈簧鋼等的淬火,高速工具鋼的預熱、中間保溫,及各種鋼的高溫回火、等溫退火等;低溫鹽浴熱處理則用於馬氏體等溫淬火、奧氏體等溫淬火、低溫回火等。
高溫鹽浴熱處理普遍使用BaCl2單質鹽浴;中溫鹽浴熱處理普遍使用NaCl、CaCl2等氯化混合鹽浴;而低溫鹽浴熱處理主要使用NaNO3、KNO3、NaNO2等硝酸鹽及亞硝酸鹽的二元系或三元系混合浴。
關於熔鹽的種類和使用溫度,從數十年前的相關資料比較得知至今仍無大的變化。目前,市場上銷售的中性鹽的使用溫度範圍大體為160-1300 ℃。而低溫鹽浴的常用溫度有時低至140 ℃。有時情況不同,也採用如下辦法:通過加入硝酸鋰(如23.3%硝酸鋰+60.4%硝酸鉀+16.3%硝酸鈉),鹽的熔點變成121℃,從而可降低使用溫度。然而因Li價格昂貴,工業上用得不多。
另外,作為回火和恆溫冷卻劑而不含亞硝酸鹽的低溫用鹽浴劑(使用溫度280-550 ℃)也已實現了商業化。
2鹽浴加熱的優越性
結構鋼、工具鋼、不銹鋼等特殊鋼的淬火大約採用750-1300 ℃的寬範圍加熱溫度。一般鹽浴熱處理廠的鹽浴淬火爐有約1000 ℃以上的高溫淬火用和中溫淬火用2種,以滿足所有鋼種的淬火溫度要求。並且,在短時間內溫度易變化是鹽浴熱處理的特點。另外,鹽浴熱處理設備佔地面積小,利用設備的組合可以滿足複雜熱處理的要求。
目前,在主流的真空熱處理和氣氛熱處理等自動化熱處理爐上,因考慮到交貨期和成本,不能進行多個客戶的不同產品混裝進行熱處理。為此,對熱處理參數進行標準化,類似熱處理條件的處理,可歸納成同一溫度和同一時間的處理。這就意味著鹽浴熱處理的最大優點是可以滿足單個或多個產品的處理要求。
大型加工件在氣氛爐和真空爐熱處理時,需要進行長時間加熱,升溫時難免發生加熱不均和局部晶粒粗大化。對此,利用鹽浴加熱的速度可達大氣加熱的4倍。如對於Φ25mm鋼棒採用氣氛爐和真空爐等輻射加熱時,到達預定溫度約需20-30min,而用鹽浴加熱僅需4min。晶粒的大小取決於在A3相變點正上方奧氏體晶粒的大小。為了盡可能獲得細小的奧氏體晶粒,對工件或鋼材進行某種程度的快速加熱是必要的條件。而鹽浴熱處理可快速均勻加熱,可確保最佳的淬火時間,從而獲得高質量熱處理產品。然而,因是快速升溫,大型工件被直接加熱至淬火溫度,有產生裂紋的危險。為此,對熱處理工件進行充分預熱是必要的。例如利用鹽浴對高速工具鋼淬火時,將Φ25mm鋼棒預熱到900℃僅需3min就消除了內外溫差,預熱到1250℃僅需2min就消除了內外溫差。
鹽浴還有一大優點,就是因處理件的表面被包覆而難以產生表層的氧化和脫碳。
但是,若在高溫鹽浴中含有水分和雜質,則會產生硫酸離子,從而引起工件腐蝕和脫碳,故須加強工藝和質量管理。而且,對於高強度鋼,利用不含水分的鹽浴處理不會產生氫脆,這也是鹽浴熱處理的優點之一。
3鹽浴冷卻優越性
對比碳素工具鋼油淬和鹽浴淬火時的冷卻曲線可知,約在170℃之前,鹽浴的冷卻速度更快。
通過高壓氣體冷卻真空熱處理爐的技術改善,目前該技術已用於相當多材質的淬火處理,但較之油冷和鹽浴冷卻,氣體冷卻的導熱係數明顯低。
與油淬等不同,鹽浴熱處理部件的均勻性優良。而且,與油淬、水淬不同,鹽浴冷卻適用的溫度範圍寬,這也是一大優點。因鹽浴冷卻無蒸汽膜階段,也就無由蒸汽膜引起的不均勻熱應力,從而可均勻地生成馬氏體,使淬火變形明顯縮小。一般低溫冷卻用鹽浴採用的鹽為硝酸鹽和亞硝酸鹽系,但因在鹽浴單質中不存在沸騰階段,較之水溶性冷媒,鹽浴在低溫區域的冷卻能力較小。並且,較之金屬,雖然熔融硝酸鹽的導熱係數不大,但較之其他液體和氣體卻要大得多。以下列出相關物質的導熱係數:Fe:80.3W.(mK)-1、Al:237W.(mK)-1、水:0.61W.(mK)-1、氦(He):0.153W.( mK)-1、酒精:0.61W.(mK)-1、空氣:0.026W.(mK)-1,硝酸鹽的導熱係數大約與水相當。
馬氏體等溫淬火用鹽浴和油的特性比較如表1所示。硝酸鹽的導熱係數約為油的5倍(以重量計算)和10倍(以容量計算)。鹽的熱容量大約為油的1.73倍。
表1 馬氏體等溫淬火用鹽浴和油的特性對比
鹽浴
|
油
| |
組成
|
KNO3、NaNO3、NaNO2
| |
使用範圍
|
150-400 ℃
|
130-220 ℃
|
密度(200℃)
|
1.92
|
0.82
|
黏度(CP)
200℃
315℃
|
7.5
2.9
|
2.9
|
比熱
|
0.37
|
0.5
|
導熱係數
Gcal/s/cm
|
1.8 ´ 10-3 ℃ /cm
|
0.39 ´ 10-3 ℃ /cm
|
熱穩定性
|
540℃
|
230℃
|
比較油和鹽浴劑的冷卻速度可知:鹽浴劑的冷卻能力在高溫區域特別優良,而油的冷卻能力在700℃以下比鹽浴的大。冷卻速度大小對晶粒細化有影響,通過相變點的冷卻速度越快,越能細化晶粒。就細化晶粒而言,採用鹽浴冷卻是有利的。
近年,對切削工具和金屬模具進行物理氣相沉積、N化、熔鹽碳化物包覆等表面改質處理增多了。此時不單是重視表面改質層的硬度及與母材的密合性,而且母材內部的硬度、韌性及尺寸穩定性也十分重要。作為對塗鍍膜密合性的評價方法之一,所進行的划痕試驗結果表明,基體硬度越高,則塗鍍層的密合性就越優良。擠壓模(又稱拉模或鍛模)鋼等淬透性好的鋼,在真空熱處理中雖能獲得充分的硬度,但即使如此,還是應少許提高硬度。
由此觀點出發,用於金屬模具和切削工具的高速工具鋼和冷、熱模具用鋼的熱處理方法就特別受到重視。適用鹽浴熱處理的高速工具鋼在處理中很敏感,其原因在於先共析(即初析)碳化物的析出溫度為1000-600 ℃,此碳化物的生成會損害材料的韌性,硬度也會下降。因此,淬火時應盡可能快地通過此溫度區間,以抑制初析碳化物的析出是很重要的。代表性高速鋼 SKH51的臨界溫度為830℃,正好是鹽浴冷卻能力充分發揮的溫度。一般在3bar的真空爐中,由於不能在此溫度急速冷卻,若工件厚度超過40mm,淬火不可避免地變慢。但在鹽浴中,此溫度區間的冷卻能力大卻變得極為有利。若在Ms點(SKH51約180℃)以下急速冷卻,雖因內外部的溫差易產生淬火應變和淬裂,但在鹽浴熱處理中,此溫度區間緩慢冷卻,對裂紋和變形的擔心還是較少的。
一般高速鋼利用鹽浴熱處理淬火,從淬火溫度浸於500℃左右的鹽浴中,因內外溫差小,空冷而可防止應變的發生。然而,若淬火時間過長,就會產生貝氏體而使韌性和硬度下降。以SKH51鋼的鹽浴淬火為例,測定了尺寸不同的處理工件中心部位的冷卻曲線,並將之記入時間-溫度轉變曲線(TTT)中,在大約Φ30mm以下的中心部位未出現貝氏體,而在直徑30mm以上的中心部位,則不可避免地析出了少量的貝氏體。
因工具鋼一般在淬火時易淬裂,故多采用馬氏體等溫淬火和限時淬火。然而,對於大型工具鋼部件,淬透性差的材料和滲C淬火部件,則要求淬火冷卻能力高的鹽浴。為此,可以攪拌鹽浴和加水以提高其冷卻能力。
在蒸汽膜可作冷卻劑的條件下,將汽膜強制崩裂雖極為有效,但即使是鹽這樣的非沸騰性冷卻劑在部件周圍流動,也會對傳熱產生大的影響。研究攪拌對冷卻速度影響可知,不攪拌時,內部會產生Ar'相變,但若攪拌程度大就不會產生Ar'相變。據此可知,對於鹽浴而言,攪拌具有重要作用。
研究水分加入鹽浴時的冷卻曲線可知,雖因研究者的不同而使最大冷卻速度的最佳水分量不盡相同,但即使加入微量的水,其攪拌效果也很明顯,且所有的情況都因加水而提高了鹽浴的冷卻能力。加水之所以能提高鹽浴的冷卻速度,主要是因為水的加入極大提高了在600-500 ℃區間的冷卻速度之故。
往鹽浴中加水雖然能提高冷卻速度,但因水會形成蒸汽膜,膜的生成和破裂會產生局部的時間偏移,從而延緩冷卻速度,並有造成應變和硬度不均的擔心。然而在實際應用中基本上未發生這樣的問題。其原因是由於加入的水量少,不能掩蓋試樣的整體表面而延緩冷卻速度。反而是因水在試樣表面的沸騰而加速了鹽的熱交換,從而促進了試樣的冷卻。
一般認為鹽浴溫度越低,其冷卻能力就越強。有研究報告指出,因水的加入可將鹽浴的熔點最大下降到80℃。
4鹽浴熱處理的應用
4.1馬氏體(M)等溫淬火
M等溫淬火是將馬氏體與回火組合的說法,但處理後的組織極少以M進行回火,其實際效果是淬火。熱浴淬火有時也是以Ms點的上或下區別分級淬火和M等溫淬火的。
M等溫淬火等技術都是從鹽浴熱處理的應用技術中產生的,標準的M等溫淬火約在Ms點以上31℃(57℉)進行,但在Ms點以下稱為改良的M等溫淬火。改良M等溫淬火一般適用淬透性差的鋼,對確保硬度方面有利,但在淬火應變和淬裂方面卻比標準M等溫淬火要差些。
M等溫淬火的缺點之一是存在殘餘奧氏體的問題。即M等溫淬火處理,在將過冷奧氏體進行馬氏體化之前,一旦中斷冷卻就會使奧氏體穩定化,從而使其硬度變低,這對長年時效變化是不利的。然而此問題通過嚴格管理相變中斷時間以及回火時間是可以防止的。
從長年時效變化考慮,作為一般的M等溫淬火不適合時的熱處理方法,應被稱作在Ms點以下保持改良M等溫淬火,即在Ms點正下方的熱浴中淬火,等溫化後升溫而急冷的操作。為防止時效,需要在Ms-Mf溫度區間急冷。
與此類似的情況也被稱作分級淬火回火處理。對比熱處理方法可作如下解說:一是在比Ms點高的等於回火溫度的熱浴中淬火;二是等溫化後升溫空冷;三是在Ms-Mf間的適當溫度升溫;四是在最初的熱浴中淬火而後充分回火操作,稱作分級淬火回火處理。此熱處理獲得低溫回火馬氏體和低溫貝氏體的混合組織,由於可用一個熱浴進行淬火與回火,故適於批量生產。目前,此法已用於高強度鋼處理。
而且,作為鹽浴熱處理的應用,渡邊等人利用將螺旋齒輪浸於鹽浴槽後,再浸於低溫鹽浴而結束相變的方法,可以將齒形變化量及波動都減半,從而獲得優良齒輪。如圖1所示,此法作為改良分級淬火(熔融鹽浴2級淬火)法而得到提倡。在一般的M等溫淬火處理中,從低溫鹽浴槽中取出後空冷處理,此時產生M相變的波動。而改良方案可以使低溫槽中的M相變更均勻,因此熱處理變形就減少了。
4.2奧氏體(A)等溫淬火處理
A等溫淬火一般適用於300-400 ℃溫度範圍。此溫度下不能使用油類,若使用Pb與Sn等金屬浴,不僅成本高,而且毒性大,故鹽浴就成了最佳選擇。
原來,A等溫淬火存在僅適用於處理小物件的缺點。其改良方案被稱作升溫A等溫淬火熱處理。這是在冷卻能力大的低溫熱浴中急冷,在未開始等溫相變的時間內取出,並立即轉移至高溫的設定溫度熱浴中進行A等溫淬火的方法。作為此熱處理的應用,受到關注的是在A等溫淬火.可鍛鑄鐵(ADI)的應用。美國在20世紀80年代就確立了自由控制ADI的組織及耐磨損性的方法。在日本,為了改善高強度、高韌性的A等溫淬火球墨鑄鐵的耐磨損性和疲勞強度,2級A等溫淬火處理也受到關注。日本學者開發如下熱處理工藝:以1級冷卻(325℃)確保硬度,為了提高切削性能而以2級恆溫保持實現了減少殘餘A的熱處理。由此可見,將第1級冷卻溫度設定為325℃,提升溫度定為400℃,將第2級恆溫保持溫度定為440℃。從而使短時間內材料中都沒有危害切削性能的殘餘A,且可以獲得目標硬度。雖然使用流化床焙燒爐也可以進行上述處理,但因其冷卻能力小,還是選定了生產實績多的連續式鹽浴爐。這樣的處理正應用於空壓機滑動部件的生產。
另外,奧氏體球墨鑄鐵件的A等溫淬火處理,過去重視韌性,而最近關注重點是改善切削性,處理多在上貝氏體相變區域進行。而且,在比韌性更受到重視的耐磨損性用途中,因在下貝氏體相變區域進行A等溫淬火處理是有效的,故已在JIS G5503中增加了新的材質。
汽車用超高強度雙相鋼和TRIP鋼,在連續冷卻轉變CCT的基礎上進行了精確的組織控制。此時雖然產生了F和B,但由於保持時間和溫度的不同,殘餘奧氏體量也有變化。因這類鋼中的殘餘奧氏體量在很大程度上左右TRIP鋼性能,故為了控制殘餘奧氏體量,須嚴格進行溫度-時間控制。針對此要求,重新對易於控制溫度和時間的鹽浴熱處理進行了評價。
即使在彈簧業界,伴隨彈簧的高性能化,也要求對其進行嚴格的熱處理。在精密彈簧上,加熱、冷卻時間都基本要求進行以秒為單位的控制。對策之一是A等溫淬火。由於在鹽浴處理中可能產生瞬間溫度波動,故可以說這是最佳的熱處理方法。
4.3 局部熱處理
在鑽、拉刀、銑刀等切削工具上,其刀尖部位須充分淬火,但其柄部有時不淬火以確保韌性。而且,有時也在刀具整體淬火後,再僅將柄部回火。這些處理方式都是鹽浴熱處理擅長的。
為了應對金屬壓鑄模的大型化要求,提高模具硬度對於改善其耐熱裂性雖是有效的,但另一方面卻增加了產生大裂紋的危險性。為此,希望降低可能成為大裂紋起點的模內冷卻孔部位(即局部)的硬度;同時,作為熱裂對策,要求提高模具表面孔穴部位的硬度。具體措施就是僅對高硬度回火的模具內面,用鹽浴進行更高溫回火,使之產生熱梯度(傾斜回火),從而使孔穴的內部硬度出現了硬度梯度,這是除鹽浴處理以外的其他處理方法難以實現的。
4.4高韌性技術和低變形化技術
利用模具整體化可進行壓鑄模的大型化,但隨之而來的冷卻孔增多,會產生熱處理後韌性不足和變形增大等新問題。這類模具用材主要是5Cr系的SKD61系鋼,此鋼即使在同等的熱處理硬度下,也會因冷卻方法的不同而使韌性明顯變化。熱工具鋼淬火時的冷卻速度與代表韌性的衝擊值的關係是:冷卻速度越小,其衝擊值越低。韌性低的原因是高溫區域的碳化物析出和低溫區域的貝氏體化。此鋼衝擊值低,除碳化物在晶界的析出外,貝氏體化的影響也很大。特別是冷卻速度越小,此傾向越明顯。關於貝氏體,若低溫區域的冷卻速度小,則貝氏體的板條寬度就會變大,這與鋼的韌性低是一致的。總之,冷卻速度越大,造成衝擊值低下的兩個因素的作用就會越弱。因此,較之氣體冷卻,鹽浴熱處理和油淬都有助於提高韌性。
關於鍛造型熱作模具鋼的淬火,以前是空冷或吹風淬火。然而,隨著模具的大型化,其冷卻會變慢,從而造成淬火不充分。因此,一直採用分級淬火,將處理工件投入油或鹽浴中急冷到Ms點正上方後,再在M相變區域空冷。
另一方面,隨著模具形狀和結構的複雜化,熱處理變形成為更為關注的問題。為了減少變形,盡可能使模具內外溫度均勻。因此,雖因高溫區域的C化物析出會對韌性有所影響,但因首先考慮的是進行變形更少的熱處理。從此觀點出發,推薦採用如下方法:一是從淬火溫度緩冷到大約600℃的方法;二是在不引起貝氏體相變的大約500-400 ℃溫度區間恆溫保持,然後利用淬火以減少熱處理變形的方法。這些方法在真空爐中實施,並成了主流,而鹽浴熱處理卻更容易。另外,試驗研究 表明,若在 550 ℃以下的溫度區間、冷卻速度在3 ℃ /min以上,就不會造成韌性大幅度下降、
4.5鹽浴裝置
鹽浴設備上有小規模自動裝置,主要包括窯爐、遙控設備和電子計算機等。自動裝置一般除採用橫向並列配置外,也採用放射裝配置。某公司開發了自動注水的M等溫淬火裝置,其後進一步改善,開發了可在180-250℃溫度鹽浴中控制最佳注水量的裝置。
美國已將氣氛爐-鹽浴、鹽浴-鹽浴兩個系統用於ADI的製造。日本也開發了連續等溫A淬火爐,及也可以處理ADI的多目的熱處理設備,現已面試。
5結語
鹽浴熱處理在效率和環境方面存在的問題仍很多,只能逐步克服。但到目前為止,其有點也是其他熱處理方式所不具備的,現狀是從環境方面考慮,鹽浴熱處理的大規模化雖然苦難,但確實嚴密的熱處理,其優越性明顯,特別是在特殊用途方面不可缺少。即使在各種新熱處理技術都進步了的21世紀,仍發揮著重要的作用。在鹽浴熱處理中現場技術人員的能力素質對熱處理質量有很大的影響。因此,一方面引進最新的技術,一方面強化技術傳承。而且,如何抓住這些環節,並長期堅持則是今後的課題。
PCB設備零組件研磨拋光前後比較
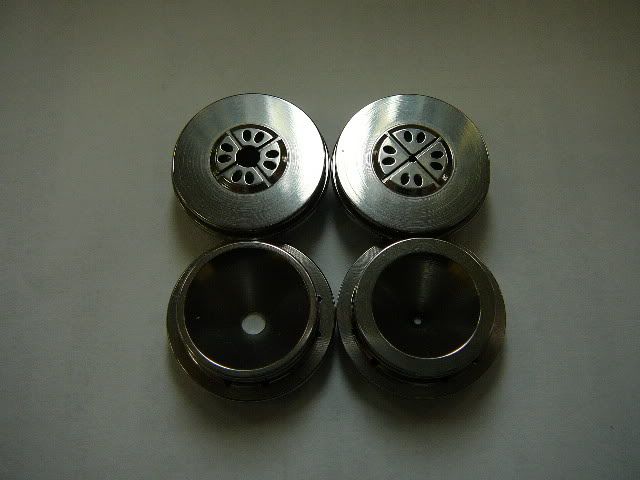
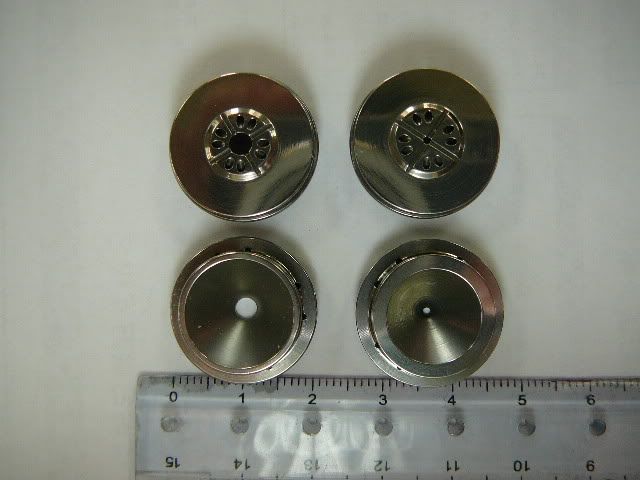
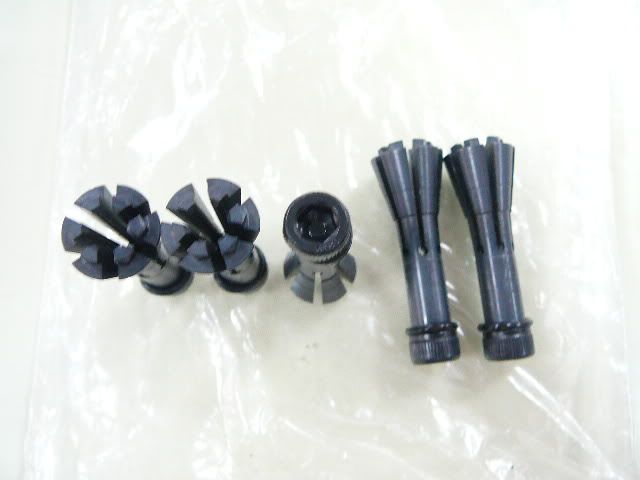
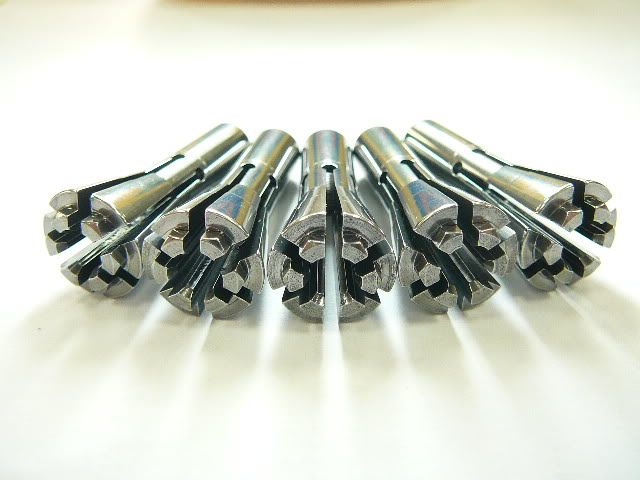
沒有留言:
張貼留言